Managing cooling and heat transfer to maintain consistent extrudate shape and quality. (function (w,d) {var loader = function () {var s = d.createElement("script"), tag = d.getElementsByTagName("script")[0]; s.src = "//cdn.iubenda.com/iubenda.js"; A pipe extrusion line consists of different parts. The material is gradually melted by the mechanical energy generated by turning screws and by heaters arranged along the barrel. Each extruded tube is pulled through a cooling bath by a precision haul-off unit. The key quality parameters in medical tube production are dimensional stability and tolerances on all dimensions. aluminum square tube Laser gages offer accurate and rapid measurement of outside diameter by measuring a shadow created when the tube obscures a fine beam of rapidly scanning light. Displacement cutters are preferred when clean, particle free cuts are required. For medical tube production lines--which demand high levels of quality and performance--it is often sensible to carry a library of screws that suit all of the materials or grades used and to introduce screw changes as a standard procedure at each material change. Research and development continue to expand the benefits of plastic extruded products for medical devices, aerospace, and recycling. Many extrusion lines utilize a series of instruments that measure extrudate dimensions in real time, then feed the dimensional information into the master process control.
In the head there is much of the secret of a good product. The profile or tube are pulled by an haul-off unit so that the line it is always in motion. The die is what gives the final product its profile or shape and must be designed so that the molten plastic evenly flows from a cylindrical profile, to the products profile shape. The challenge for manufacturers is to find the optimum processing conditions enabling each grade to produce high-quality, close-tolerance tubing capable of being run in a single operation at acceptable outputs. The last step is the cutting unit, which also depends on much of the type of product that is manufactured. Properly preparing and drying certain plastics that adsorb moisture that can cause quality problems for medical-grade or commercial applications. This type of screw, if well-designed, ensures complete melting, often over a reduced length of screw, and offers enhanced mixing due to the high levels of shear developed through the barrier clearance. It is important that the iron content be kept to less than 1% so as to eliminate melt contamination caused by iron-based specks that can form in corrosive environments.

In the immersion the tube passes through a water-filled container in constant cooling. With PVC and PUR, however, reversion specifications are critical, and reversion reduces with lower drawdown ratios. Informa Markets, a trading division of Informa PLC. crosshead extrusion 2022 Hi-Tech Extrusions. Dies should be designed for uniform flow of material, producing uniform product with minimal internal stresses. In order for a manufacturer to offer precision medical tube products, the various parts of the extrusion process need to be operated under optimized and integrated conditions. The first system is used for pipes with large diameter, where production speeds are low and the spray can achieve effective cooling. This is a sector which has much relevance.
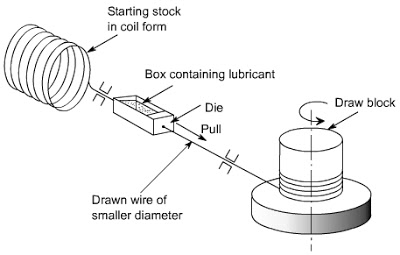
Thus, the design and manufacture of small-diameter PVC or PUR tubing becomes more difficult. Reliably delivering materials to extrusion lines, without contamination or moisture regain, and mixing in precise levels of process regrind to minimize process material waste. In-line granulation systems may be essential for managing continuous, high-volumes of scrap, while other processing operations may be able to keep pace by collecting scrap and granulating it off-line, either in machine-side or centralized granulation systems, with output stored as regrind that can be reprocessed later. The rotating screw forces the plastic resin forward into the barrel that is heated to the desired melt temperature depending on the resin. To learn more about auxiliary equipment needed to support extrusion or for help in developing an extrusion line, you can contact Conair here. Auxiliary equipment is vital to: Extrusion lines are typically spoken of as having two parts or sides: Upstream and Downstream. Once cooled, it pass to the Haul off unit, which generates all the strength which, to put it in some way, pulls the profile or tube in order to extract it from the extrusion line. When you consider how hot material can get sitting in a silo during the summeror how cold it could be in the wintertaking the opportunity to pre-dry and homogenize incoming material can make a big difference in part quality all year around. And, the most cost-effective way to buy bulk resin is by railcar or truckload quantity. Smaller resin deliveries can be moved to smaller capacity storage areas, such as surge bins, or over shorter distances using a cycling loader.
You can see how this popup was set up in our step-by-step guide: https://wppopupmaker.com/guides/auto-opening-announcement-popups/, Plastic films used in construction, agriculture, packaging or other applications, Rigid or flexible plastic sheets, sheet-based construction or packaging products, thermoformed products, Plastic siding, plastic lumber or plastic/composite decking materials, Plastic profiles for window frames, housings, moldings, or decorative purposes, Flexible plastic tubing for medical, industrial or domestic applications. Today's extruded medical products require the careful application of precision processing concepts, especially for multilumen, microbore, coextruded, or cross-head- extruded tubes, for which the diameter tolerances can be as small as 5 m. Increasing product accuracy will lead to significant reductions in material usage and resultant cost savings. There are signs that, in the near future, this real-time control may allow for "intelligent processing" in the demanding field of precision small-diameter medical tube production. By spray or immersion baths you can cool it down. The mixing performance of the screw is very important in ensuring sufficient gel reduction to promote high clarity. In the case of fluoropolymers, Hastelloy C should be used for all components likely to come into contact with the molten material. In this process, the polymer melt enters the die at right angles to the outlet, which allows lumen characteristics to be controlled by individual, pressurized air supplies fed from the back of a cross-head die and into the tube via precision-bore injector needles. And then, we got to the cooling tank that eliminates the residual heat of the pipe that remains at the exit of the calibration tank. Informa PLC's registered office is 5 Howick Place, London SW1P 1WG. Outside diameter is controlled by vacuum calibration. When the data are viewed statistically, deviation trends can be seen, allowing process adjustments to be made by a control feedback loop. The stripes are produced by coextruding another material into the tube die from a second extruder. The melt gear pump consists of a pair of precision-ground, closely intermeshing gears and acts as a positive-displacement pump to supply melt at a set volumetric rate. In Western Europe and the United States, the advent of better health care has resulted in a higher proportion of both very young and aging populations--groups that form the majority of those receiving treatment by invasive surgical and after-care techniques. Additives, such as colorants and UV inhibitors, in either liquid or pellet form are often used and can be introduced into the resin below arriving at the hopper. film edge trim, thermoform blanks, sheet trim, or pipe scrap) into re-usable material. Extrusion creates product continuously through the constant rotation of the resin compressing screw. These stresses can cause warping upon cooling. Todays sessions include presentations on Industry 4.0, smart resin conveying, trends in the plastics medical device market, and Conairs new common control platform. Immersion or water-spray cooling tanks transfer heat out of the extrudate as it forms so that it can cool, shrink, and harden into its finished dimensions. swaging process diameter metal reduce tubes efunda processes processing Plastics Extrusion in advanced manufacturing is not simply choosing different colors to push through several basic shapes Custom Plastic Extrusion can combine the properties of advanced materials to enable specific performance characteristics for plastic tubing or plastic parts, and can form multi-lumen tubing or complex profiles to fit a wide range of applications for commercial, industrial, food processing, filtration, automotive, military and medical/pharmaceutical industries. In the case of corrugated pipes, vacuum calibration use the same principles as for the smooth tube. Delivering such blends consistently and continuously is the job of feeding, mixing, and blending equipment. A breaker plate generally reinforces screens because the pressure at this point can exceed 5000psi(34MPa). Unless "mopped up" by heat stabilizers, these "chain-scission" reactions result in discoloration and rapid thermal degradation at around 230C. That is because internal moisture in these resins can cause voids, discoloration, holes, or structural weakness in injection molded parts, resulting in diminished performance and appearance properties and, ultimately, scrap. There is no such thing as a "general-purpose" screw. Many resins can be compounded with optical or x-ray opacifiers such as titanium dioxide, barium sulfate, or bismuth subcarbonate, further increasing the number of potential materials and grades. Do you remember as a kid shoving play dough into the red and yellow toy to squeeze out a rope shaped like a star or a flower? Probes measure wall thickness at a single point around the tube; a number of probes can be used if measurements of multiple points around the diameter are required. The 3-day virtual conference for plastics processors begins today! There are two principal methods used for controlling the shape of each lumen. Any two of the product dimensions may thus be controlled at any one time. The matching of extruder screw design to the melting and rheological characteristics of the plastic to be processed is fundamental to extruder performance. Betol manufactures twin screws for compounding and complete extrusion lines for the production of fine-tolerance tubing and multilayer film and sheet. Magazine | MPB Article Index. The extrusion process would not be possible without the use of multiple types of auxiliary equipment upstream and downstream from the extruder. A puller is a motorized device that uses rotating belts or cleated tracks to pull extrudate through downstream equipment at a precise, finely adjustable speed. In the plastics extrusion process, rawthermoplasticmaterial, or resin, is gravity fed from a top mountedhopperinto the barrel of an extruder. Here are a few examples: Whatever the process, it is essential to size granulation systems and accessories to deal with scrap volumes effectively without process disruption. Cooling equipment varies based on the application: Larger extrusions, including pipe and decking, often use spray-cooling, while smaller flexible tube products use immersion cooling, often in vacuum cooling tanks. Data can be gathered (typically at 100 scans/sec) and rapidly converted by a process controller to provide waveform readings or live trend charts. But because film scrap is very light relative to resin pellets, it doesnt mix uniformly when reintroduced for processing in a conventional blender. Leave us you contact and we will send you soon the access to our high resolution virtual tour that provide a realistic and immersive way to show Bausano facilities and operations.
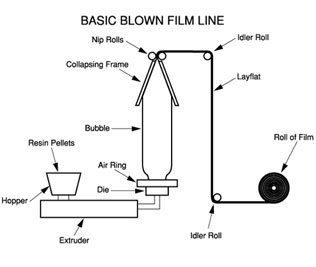
As noted earlier, some high-volume extrusion processes, such as film extrusion, produce significant amounts of scrap material continuously, while others produce occasional scrap resulting from changeovers, interruptions, or variances that result in rejected products. In many cases, these tools extend right into the cooling equipment. TCUs support the cooling process, providing a steady flow of tempered water to cooling and spray tanks so that they can maintain a constant coolant temperature and a consistent rate of heat transfer as extruded product moves continuously through the cooling process. Secondary operations, such as drilling holes or further shaping, add functionality. Plastics are excellent thermal insulators and are therefore very difficult to cool quickly. Predrying of hygroscopic or moisture-sensitive materials--for example, polyurethanes, polyamides, and polyesters--is essential, particularly if high levels of inorganic filler are present. In most processes, a heating profile is set for the barrel utilizing three or more independentPID (proportional-integral-derivative controller) controlledheat zones that gradually increase the temperature of the barrel from the rear where the resin has entered to the front. Here we will focus on the high output use of plastic extrusion to form plastic parts that we use on an everyday basis and for industrial and medical processes. Such products are part of the increasing trend toward minimally invasive surgery, examination by miniaturized optics, or microsurgery using laser techniques. Of course, consistent moisture removal is essential for processing any hygroscopic resin (i.e., PET, polycarbonate, ABS, nylon, etc.). Plastics have been used in medical devices for more than 40 years, from the time that plasticized PVC first replaced natural rubber and glass. An advantage of extrusion in manufacturing is that a product can be produced continuously with high output in a conforming shape and then reeled for applications requiring continuous product such as tubing extrusion, pipe extrusion, or film; or parts are cut with high precision to various lengths as needed for a wide variety uses. In performing all of these vital roles, properly functioning auxiliaries address and eliminate a wide range of material, temperature, and process inconsistencies that can cause many common extrusion problems. Multiple TCUs and larger cooling circuits may be served by higher-capacity portable or central chilling units which provide much higher levels of chilling capacity. Extruders are available in a huge range of output capacities and types to accommodate different materials. When choosing the cutting system must be taken into account the diameter and wall thickness, the raw material used, the shape, quality and the length of the cut. 2022 PBS Plastics. The relative flow rate required to maintain lumen size at a given die speed can be computed, but care must be taken to ensure that the air supply used for pressure regulation is subject to the same influences as the ambient air surrounding the extrusion line. To give you the best possible experience, this site uses cookies and by continuing to use the site you agree that we can save them on your device. Accepting and shaping hot extrudate into precise dimensions while maintaining consistent process speed. Reusing the large amounts of process scrap produced in some extrusion lines can pose a serious blending challenge. Single or Twin screw extruders are used for pipe manufacturing. Thermoform extrusion processors may also require continuously-running, automatically fed granulation systems to prevent the accumulation of blanks from cluttering or delaying thermoform production. Dual-plane laser gages measure OD in two planes, providing both average OD and ovality with a resolution of 1 m. SPC control-group data and functions can be used to improve the process capability indices relating to a product's dimensional accuracy (see Figure 6). Examples include taking/giving sets (for transfusion, infusion, dialysis); catheters (intravenous, cardiovascular); endotracheal tubes (for intubation or anesthesia); tracheostomy tubes; and cystoscopy instruments. Copyright 2022. Therefore, the first step is to determine how to measure quality, and then identify which process variables can be manipulated to influence that quality. As the material enters the feed throat near the rear of the barrel it comes in contact with the screw. Well work with you personally to ensure that your order is designed, extruded, and shipped correctly the first time. drawing tube process wire sinking plug accurate simplest least option using While injection molding can offer many similar profiles in continuous lengths, usually with added reinforcing, the finished product is pulled out of a die instead of extruding the fluid resin through a die. To ensure that a manufacturer's multilumen tubing will sustain precise flow levels, the extrusion process must include some means of maintaining the consistency of all tube dimensions. The product must now be cooled which is usually achieved by pulling the extrudate through a water bath. Obviously, extrusion processing capabilities rely first on having an extruder that is sized and equipped to provide the right type and volume of plasticized polymer (extrudate) to a process, whether that process involves making film, tubing, pipe, profiles, or sheets. To move material (virgin pellets, post-consumer recycled pellets, regrind) from in-plant storage locations to extruders and auxiliary equipment like dryers or blenders, processors rely onvacuum conveying systems. Every extruder relies on a master extrusion control that regulates not only its operation and output, but the speed of the downstream equipment. A considerable variety of materials are available for medical tube extrusion, with properties to satisfy most end-user requirements while meeting strict regulations relating to biocompatibility and nontoxicity. Precision tube products must be made correctly the first time, every time. A white drinking straw that has two colors of stripes, requires a total of three extruders to manufacture. The process has much in common with plastics injection molding though differs in that the process is usually continual.
The difference in pressure caused, shapes the surface of the plastic pipe pushing it against the system, providing the product the required corrugation. And dont miss the live Q&As! Gamma backscatter probes use gamma-radiation backscatter to determine wall thickness down to 0.05 mm (with a resolution of 1 m) for tubes with diameters as small as 1 mm. A typical tolerance range is 1%, which for a tube with an internal diameter of 1.6 mm translates to accuracies of 10 m (the diameter of an average human hair is only 75 m). For example, a coextruded tube could have an internal hardened tube through which a cable can be run along with a flexible outer layer to maintain maneuverability. For example, film extrusion lines continually produces so much edge trim they require in-line granulation systems that capture and process film scrap immediately (see Downstream equipment below).
The extruder itself is the last element of the upstream process. Measuring, cutting, coiling and collecting a continuous flow of finished extruded product.
