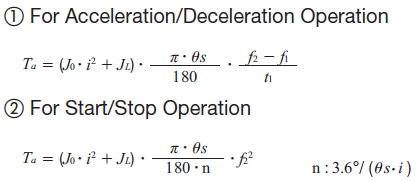
Z = total no. Frame 2: The top electromagnet 1 is deactivated, and the right side electromagnet 2 will be activated, pulling the teeth into alignment with it. Hence, the motor speed ( ) will be: = ( steps per second / steps per revolution ) 60 = ( 30 / 500 ) 60 = 3.6 RPM. State some applications of stepper motor. Although there are a number of different components within a stepper motor that have a large impact on performance, it can be argued that the most important
a = step angle fz = pulse frequency in hertz Example 1: Drive step resolution is set for 1000 steps per revolution. torque acceleration required orientalmotor The step angle is determined by the formula: Step angle = 360 degrees / N where N = (NPH x PH) NPH: Number of magnetic poles for each phase. There are various designs of stepper motors available. Generally speaking the top speed of a stepper motor is approximately 1000rpm. Basic Motor Information. Formula: step per inch = (motor steps * microstepping) / (travel at one turn of the motor in inches) if microstepping is set at 16 (1/16 on the driver) then and you are using a sprocket and chain with a pitch of .25 inches and 12 teeth on the drive sprocket. 5. calculate RPM of a stepper motor | All About Circuits Speed and Pulse Frequency of Stepper Motor Stepper Motors How to calculate the speed of a stepper motor - Forum Torque - speed curves are generated by plotting motor speed, armature current, mechanical output power, and efficiency as functions of the motor torque. In other words, the stepper motor can go from 0 to this speed in no time. However, although the pulse frequency is increased, the speed is increased, but the torque is lost. - Speed Variation Ratio 1/64 => gear ratio, output shaft is driven via a 64:1 gear ratio. conductors in armature. The basic formula is very similar to one that almost everyone knows: F=MA which says that force is equal to mass times acceleration. motor slip formula speed including figure automatedbuildings track This will be specified by motor manufacturer too. I= 2*Imax. While it is true that changing the voltage changes the rate of current charge across the windings and thus the maximum speed the stepper can reach, the motor speed is set by the rate at which the cur- How are stepper motors controlled? - Speed control of Using the following formula you can determine your voltage needed. We can calculate the an induction motor speed using the speed formula as given below. stepper motor speed - machsupport.com screw speed critical lead formula power mechanical formulas calculator calculate calculations engineering ncalculators Synchronous, Stepper and AC Motors Formulas and So without reducing time t2 how can i maintain the same frequency for various speed as like in DC motor. 2-4-3. Characteristics of Stepping Motors | Nidec Corporation Most stepper motors require gradual ramping to full speed. The hybrid stepper motor is more expensive than the PM stepper motor but provides better performance with respect to step resolution, torque and speed. Step Motor With Acceleration and End of Stroke - Instructables Fig. Simply, we have provided a formula: v=f/n. This parameter is governed by mechanical design of the stepper motor. Stepper Motor Calculations - CNC.xyz Wiki Understanding how much power a stepper motor draws Stepper You cannot vary the speed without changing the pulse frequency. Stepper motors. There are various designs of stepper motors available. T= I*L/V. Motor Speed (RPM) = (f *60*2) / p. Where f is source frequency in Hz. n: number of microstep, you can find it on stepper driver. eg. When stepper motor driver receiving frequency 4000pps from controller, and mircostep setting on the driver is: 2000, the speed of motor is: v=4000/2000=2rps=120rpm Stepper motors are similar, following Newtons famous law F = ma. rate. That assumes that the load does not exceed the torque limit and result in missed steps. How much speed can you get with a stepper motor & controller? As we have seen that in half mode, the number of steps taken by the motor to complete one revolution gets doubled, so step angle reduces to half. motor stepper current formula max bridge pyroelectro tutorials maximum control My motors are connected directly to a 5TPI screw. Characteristics of Stepping Motors. stepper motor torsion gearheads harmonic formulas angles obtained individual The motor's position can then be commanded to move and hold at one of these steps without any feedback sensor (an open-loop controller), as long as the motor is carefully sized to the application in respect to torque and speed. Check the current with the formula: U=IxR Next we will look at the critical screw speed which can be found using the following equation: n c [rpm] = C s 2x 1 The most simple type of stepper motor is a two phase unipolar stepper motor 32 * (mH inductance) = Power Supply Voltage If your motor has 2mH of inductance, the equation would look as follows Description: stepper
Stepper motor Here is the lib StepMotor, which is a library that I made, which manipulates the 8825, 4988 and TB6600 drivers, and allows you to play larger engines like the Nema 23 or 34, for example. This formula is the synchronous speed while the motor at full load will be slightly lower in speed than this. 10. Let / f 0 = , that is, the decrement of two adjacent pulse periods in the acceleration stage, the above formula is simplified to: t n = (n-1) T 1 (n-2) (n-1) / 2 (4) It is defined as the number of steps needed to complete one revolution of the rotor shaft. 2.57 shows the relationship between the torque and speed of a stepping motor by taking the torque on the vertical axis and the pulse frequency on the horizontal axis. the motor need 360/1.8 step for a full rotation = 200 step/pr (pr : pour rotation) now let calculate linear displacement for each step ( you can do Re: Stepper motor doubt The motor seems to have a 100:1 gear, provided a pulse in "200 pps" means a full step. Speed 6. Hello people of the internet, I'm working on a project that involves a large (1600mm dia) turntable capable of carrying a maximum load of 300kg. The motor interface type must be set to 1 when using a step and direction driver. Two curves are drawn in the figure. To compute maximum revolutions per second - divide seconds per step by steps per revolution. If you are actually using 2 phase steppers with a maximum of 4.5 A (the capability of the controller), then you might expect 4.5^2 * 0.6 = 12 W per phase. The emf equation of DC motor is given by. A simplified overview of the physics of high speed stepper motor operation. [May 2017]
eg. n = q * Hz / (360 * D) n: rev/sec. A single-stack, 8 phase (stator), multiple-step motor has 6 rotor teeth. Rev/sec = V/ (L*2*Imax)/ (steps/rev) motor stepper stack reluctance multi variable equation rotor stator hence represented tooth pitch shown below FAQ: What are the requirements for stepper motor acceleration? To stop, the motor speed is then reduced until it is below the pull-in torque curve. With stepper motors, however, changing the voltage does not have any effect on the motor speed. Stepper Motor, Construction, Working, Types & Applications You can't. Unlike AC or DC motor that rotates continuously, stepper motor rotates in steps. Stepper Motor Calculator.
400 steps/second would give 60 RPM, and 200 sps would give 30 rpm. Usually this will be specified by the motor manufacturer. Stepper However, a slightly different formula is used to calculate the maximum speed of a stepper motor. As a consequence, the current can be deducted from the previous formula as shown in equation 3. Define resolution. torque motor dc armature mechanical speed relationship calculator formula between calculation emf power calculate motors theoretical formulas example output refer Setting a velocity limit will prevent the stepper motor from stalling. The exact speeds that are possible depend on the specific motor being used and the controller being used with it. Hence, the motor speed ( ) will be: = ( steps per second / steps per revolution ) 60 = ( 30 / 500 ) 60 = 3.6 RPM. Stepper motors are controlled by a driver, which sends the pulses into the motor causing it to turn. 8. torque kgcm drehmoment force kreuzprodukt abstand Step Sequence of Stepper Motor - IDC-Online The basic formula is the same for all motors. Speed up a stepper motor motor dc current inrush calculate calculation limit ametherm watts three horsepower The step angle for a 3-phase, 24 pole permanent magnet stepper motor is. An electric motor is an electrical machine that converts electrical energy into mechanical energy.Most electric motors operate through the interaction between the motor's magnetic field and electric current in a wire winding to generate force in the form of torque applied on the motor's shaft. The inductive nature of the motor winding is now obvious. IP22 rated medical & home-healthcare 18/24/36W AC-DC adaptors with interchangeable AC plugs. A standard stepper motor will have a step angle of 1.8 with 200 steps per revolution. speed motor synchronous induction formula calculator ac calculate example electrical formulas sub ncalculators T= L*Imax*2/V. That means you need a torque of 2.115Ncm to accelerate at 1800 mm/sec2 a mass of 2.5 kgm. Check the current with the formula: U=IxR Next we will look at the critical screw speed which can be found using the following equation: n c [rpm] = C s 2x 1 The most simple type of stepper motor is a two phase unipolar stepper motor 32 * (mH inductance) = Power Supply Voltage If your motor has 2mH of inductance, the equation would look as follows Description: stepper formula
Stepper Motor Calculator - Electrical Engineering & Electronics Tools Each step represents 1.8, or 200 steps per revolution. Stepper Motor Calculator | Do Supply Tech Support Industrial Circuits Application Note Stepper Motor Basics What is the maximum speed (highest frequency) of the stepper STEPPER MOTOR The first step is to include the library with #include