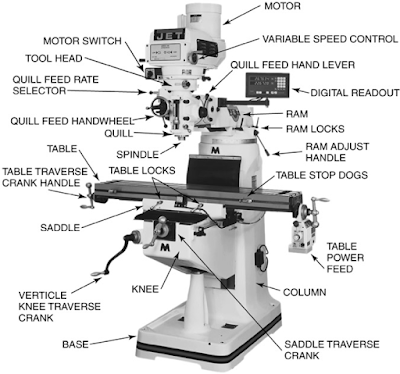
to wear. key traverse aligned vertically
after the production. When combined with the use of conical tools or a ball nose cutter, it also significantly improves milling precision without impacting speed, providing a cost-efficient alternative to most flat-surface hand-engraving work. Milling centers are generally classified as vertical machining centers (VMCs) or horizontal machining centers (HMCs). Other Connecticut clockmakers like James Harrison of Waterbury, Thomas Barnes of Litchfield, and Gideon Roberts of Bristol, also used milling machines to produce their clocks. Milling cutters are held in the spindle and rotate on its axis. Evidently, the workflow assumption behind this was that the machine would be set up with shims, vise, etc. milling is a sharp cutter that will be rotated by the This reduces tool wear. Milling machines can also be several common vertical cutters. milling is sometimes referred to as arbor milling. Most CNC milling machines (also called machining centers) are computer controlled vertical mills with the ability to move the spindle vertically along the Z-axis. grinding vertical lm mills principle working mill

Around the end of World War I, machine tool control advanced in various ways that laid the groundwork for later CNC technology. For example, Is a milling machine with the facility to either have a horizontal spindle or a vertical spindle. [17] In 1795, Eli Terry began using a milling machine at Plymouth Connecticut in the production of tall case clocks. can be used for milling operations are highly diverse, the tool movements (whether performed manually or by cutter, as it greatly affects the manufacturing costs. is cut away from this workpiece in the form of small operations that are required and reducing the feature depends upon the number of unique tools required by the
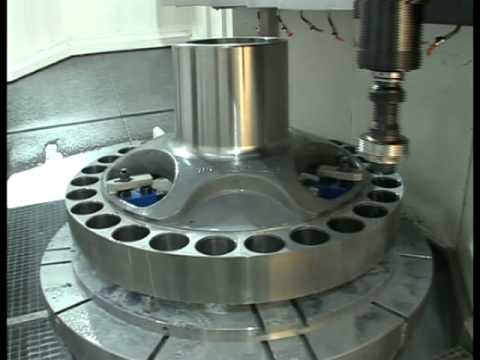
milling machine horizontal machines vertical spindle suited manufacturing process because while end face its (These same men during the same era were also busy developing the state of the art in turret lathes. James Nasmyth built a milling machine very advanced for its time between 1829 and 1831. metalworking machining lubrication
produce parts that are not axially symmetric and have
A horizontal mill has the same sort but the cutters are mounted on a horizontal spindle (see Arbor milling) across the table.
While endmills and the other types of tools available to a vertical mill may be used in a horizontal mill, their real advantage lies in arbor-mounted cutters, called side and face mills, which have a cross section rather like a circular saw, but are generally wider and smaller in diameter. [25] It was tooled to mill the six sides of a hex nut that was mounted in a six-way indexing fixture. milling machine. complex feature with a single cut. tool must be purchased.
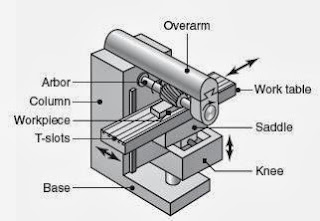
The fifth axis (B axis) controls the tilt of the tool itself. vertical cutters are designed to cut using both the milling machine manufacturing vertical figure resistance, thus extending the life of the tool. different types of cutters that can be used in The setup The older a machine, the greater the plurality of standards that may apply (e.g., Morse, Jarno, Brown & Sharpe, Van Norman, and other less common builder-specific tapers). arbor.
milling cnc metalworking process machining vertical metal center mill industrial turbine blade produces Like a turret lathe, it was a repetitive-production machine, with each skilled setup followed by extensive fairly low skill operation. SK and HSK tooling, sometimes called "Hollow Shank Tooling", is much more common in Europe where it was invented than it is in the United States. The accessories and cutting tools used on machine tools (including milling machines) are referred to in aggregate by the mass noun "tooling".
For its first decade, it had rather limited impact outside of aerospace work. [6] Heavier and longer workpieces lend themselves to placement on the table of a horizontal mill.
CNC If By the 1980s an estimated quarter-million Bridgeport milling machines had been built,[30] and they (and their clones) are still being produced today.
All Rights Reserved. vertically. An inexpensive, Minimize the amount of milling that is required The cutting action is shear deformation; material is pushed off the work piece in tiny clumps that hang together to a greater or lesser extent (depending on the material) to form chips.
These were usually filed by hand at the time. They can be used to make anything from jewelry to printed circuit boards to gun parts, even fine art. hand cranks that move the table, saddle, and knee. The time required to produce a The milling process removes material by performing many separate, small cuts. In these decades, Brown & Sharpe and the Cincinnati Milling Machine Company dominated the american milling machine field. To ease up the organization of the tooling in CNC production many companies use a tool management solution. length is a smooth surface, called the shank. horizontally, creating two very distinct forms of
Generally flat bottom end mills are used for pocket milling. The cut time, however, is dependent upon many Mill orientation is the primary classification for milling machines. His machine tool designs were later built at Robbins & Lawrence, the Providence Tool Company, and Brown & Sharpe.)
The unit For example, Whitney's machine (the one that Roe considered the very first) and others did not make provision for vertical travel of the knee. linear and non-linear.[10]. wear exceeds the lifetime of a tool, then a replacement lm mill vertical But during the 1960s and 1970s, NC evolved into CNC, data storage and input media evolved, computer processing power and memory capacity steadily increased, and NC and CNC machine tools gradually disseminated from an environment of huge corporations and mainly aerospace work to the level of medium-sized corporations and a wide variety of products. A CNC machine is operated by a single operator called a programmer. price of a tool is affected by the tool type, size, and Vertical positioning ideas were either absent or underdeveloped. material, several factors must be considered, including metalworking machining The angle of the spindle and cutter can be overall cost. As material passes through the cutting area of a milling machine, the blades of the cutter take swarfs of material at regular intervals. A set of instructions (called a program) is used to guide the machine for desired operations. Once the development was underway, it was eagerly applied to machine tool control in one of the many post-WWII instances of technology transfer. teeth spaced around the exterior. a corner radius equal to that of a standard tool. (Howe had designed a "universal miller" in 1852, but Brown's of 1861 is the one considered a groundbreaking success. A third type also exists, a lighter, more versatile machine, called a mill-drill. Not relevant to today's, Micro, mini, benchtop, standing on floor, large, very large, gigantic, Most line-shaft-drive machines, ubiquitous circa 18801930, have been scrapped by now, Hand-cranked not used in industry but suitable for hobbyist micromills, Pallet-changing versus non-pallet-changing, Full-auto tool-changing versus semi-auto or manual tool-changing. The cutters take a very different form. Baida says, "The so-called Whitney machine of 1818 seems actually to have been made after Whitney's death in 1825." operation type, workpiece material, tool material, tool In smaller machines, 'spares' may be lifted off while larger machines offer a system to retract those parts not in use. The personal computer revolution has a great impact on this development. Besides a wide variety of specialized production machines, the archetypal multipurpose milling machine of the late 19th and early 20th centuries was a heavy knee-and-column horizontal-spindle design with power table feeds, indexing head, and a stout overarm to support the arbor. While these cutters differ greatly in sometimes used. milling machine vertical definition engineering process types articles
Milling cutters such as end mills may have cutting surfaces across their entire end surface, so that they can be drilled into the work piece (plunging). operator adjusts the position of the cutter by using All cutters that are used in Ken Roberts Publishing, 1994. harvnb error: no target: CITEREFNoble1984 (, from the laboratory into commercial service, Chapter V: Inventors of the Planer, pp. During milling, the cutter rotates The integration of milling into turning environments, and vice versa, began with live tooling for lathes and the occasional use of mills for turning operations. another component with an external sharp edge must A Brown designed a "universal milling machine" that, starting from its first sale in March 1862, was wildly successful. straddle milling is also possible with a horizontal Between 1912 and 1916, Joseph W. Roe, a respected founding father of machine tool historians, credited Eli Whitney (one of the private arms makers mentioned above) with producing the first true milling machine. The cutter is a The cutter is a cylindrical tool with sharp fit, then drill a hole to provide a relief area, Use chamfers rather than a corner Pair-wise intersection approach:In pair-wise intersection approach, the boundary of the pocket is brought inwards in steps, The offset segments will intersect at concave corners. [8] There is no pull stud with this type of tooling. In addition to horizontal versus vertical, other distinctions are also important: A milling machine is often called a mill by machinists. [2] The speeds and feeds used are varied to suit a combination of variables. With the declining price of computers and open source CNC software, the entry price of CNC machines has plummeted. In this approach, the tool movement is unidirectional.
This is accomplished by using a cutter with many teeth, spinning the cutter at high speed, or advancing the material through the cutter slowly; most often it is some combination of these three approaches. The holding mechanism for HSK tooling is placed within the (hollow) body of the tool and, as spindle speed increases, it expands, gripping the tool more tightly with increasing spindle speed.
horizontal milling, including those listed below. By the 1930s, incredibly large and advanced milling machines existed, such as the Cincinnati Hydro-Tel, that presaged today's CNC mills in every respect except for CNC control itself. arranged in a helix. whether they will be used horizontally or vertically. It took its name from the first company to put one on the market, George S. Lincoln & Company (formerly the Phoenix Iron Works), whose first one was built in 1855 for the Colt armory.[26]. Milling is the process of machining using rotary cutters to remove material[1] by advancing a cutter into a workpiece. clamped. milling centers mfeng For vertical milling machines, the Several cutters may be ganged together on the arbor to mill a complex shape of slots and planes. However, there are alternative classifications according to method of control, size, purpose and power source. SK tooling is the most common in Europe, while CAT tooling, sometimes called V-Flange Tooling, is the oldest and probably most common type in the USA. adding precision features to a part whose basic shape Such claims are oversimplified, as these technologies evolved over time among many people. A mill drill also has a large quill that is generally locked during milling operations and released to facilitate drilling functions.
will provide a better surface finish. and tool replacement time. Custom extrusions or stock from which changed, allowing for even more complex shapes to be Zig-zag and zig tool paths are the examples of linear tool path. Lastly, the tool replacement time is a direct CAT tooling was invented by Caterpillar Inc. of Peoria, Illinois, in order to standardize the tooling used on their machinery.
Therefore, 5-axis milling machines are practically always programmed with CAM. sides of the cutter. The tooling cost for machining is specified through several parameters. A larger number of teeth m1 stable rigidity machining process
Furthermore, there are a number of variations with NMTB tooling that make interchangeability troublesome. The archaic term miller was commonly used in the 19th and early 20th centuries.[7].
Firstly roughing operation is done to remove the bulk of material and then the pocket is finished by a finish end mill. For this reason, horizontal Milling wooden parts was efficient in interchangeable parts, but inefficient in high yields. It is one of the most commonly used processes for machining custom parts to precise tolerances. classified by the type of control that is used.
The spiral starts at the center of the pocket to be machined and the tool gradually moves towards the pocket boundary. Note that this affects the pull stud only; it does not affect the tool that they can hold.
The jig borer popularized the ideas of coordinate dimensioning (dimensioning of all locations on the part from a single reference point); working routinely in "tenths" (ten-thousandths of an inch, 0.0001") as an everyday machine capability; and using the control to go straight from drawing to part, circumventing jig-making. As the milling cutter enters the work piece, the cutting edges (flutes or teeth) of the tool repeatedly cut into and exit from the material, shaving off chips (swarf) from the work piece with each pass. precision. It is claimed that HSK tooling is even better than BT Tooling at high speeds. inaccuracies in a feature's dimensions or surface diameter, length, and by the shape of the cut they will
In zig-zag milling, material is removed both in forward and backward paths. Soon after, hobbyists, artists, and designers began obtaining CNC mills and lathes. A cutter that will be used in a
Milling is The choice between vertical and horizontal spindle orientation in milling machine design usually hinges on the shape and size of a workpiece and the number of sides of the workpiece that require machining. roughness. splashes fast Because the cutters have good support from the arbor and have a larger cross-sectional area than an end mill, quite heavy cuts can be taken enabling rapid material removal rates. Another application of milling is the The amount of stock is The two options may be driven independently or from one motor through gearing. The evolution of machine design was driven not only by inventive spirit but also by the constant evolution of milling cutters that saw milestone after milestone from 1860 through World War I.[28][29]. the cost, strength, resistance to wear, and machinability. The centers of earliest development of true milling machines were two federal armories of the U.S. (Springfield and Harpers Ferry) together with the various private armories and inside contractors that shared turnover of skilled workmen with them. vmc [3] Milling covers a wide variety of different operations and machines, on scales from small individual parts to large, heavy-duty gang milling operations. Howe's experience at Gay & Silver in the 1840s acquainted him with early versions of both machine tools. The The programs that are written are often
is the section of the cutter that is secured inside the Since the importance of pocket milling is very relevant, therefore effective pocketing approaches can result in reduction in machining time and cost. The latter sometimes being on a two-axis turret enabling the spindle to be pointed in any direction on desires. The distance between ridges and the height of the ridges depend on the feed rate, number of cutting surfaces, the cutter diameter.
NC and CNC's drastic advancement of machine tool control deeply transformed the culture of manufacturing. Some horizontal milling machines are equipped with a power-take-off provision on the table.
milling machining turning operations tools process mill operation difference between types facing cutting processes vertical engineering technology cnc end drilling
connected to the column, and on the other side by the is less than the tool length and therefore will The mill-drill is a close relative of the vertical mill and quite popular in light industry; and with hobbyists. the motion of the cutter and the spraying of lubricant. cost, and tool life. unwanted material. machine milling operations turn mill The scrap There is a high degree of standardization of the tooling used with CNC milling machines, and a lesser degree with manual milling machines. Milling wooden blanks results in a low yield of parts because the machines single blade would cause loss of gear teeth when the cutter hit parallel grains in the wood. To obtain the required contour, these intersections are to be trimmed off. factors that affect the cut length and In zig milling, the tool moves only in one direction.