The arc length is the distance between the pool of molten metal and the wire at the point of the arc.
The second problem is that your shielding gas will no longer be able to reach your weld pool, and youll increase the number of defects like porosity in your weld. O.K. You are probably here for this reason, so Ill explain the main MIG settings and how they should be adjusted.
Some welding machines claim to weld 3/8-inch steel with only 170-200 amps.
Before you can even start, you have to choose the right process and take care of the mechanical and technical setup.
Youll usually need to increase your travel speed and lower your amps to keep the molten metal from dripping, so while youre learning, flat positions are best.
Thanks for the explanations, they helped alot. Because MIG welds do make spatter, and if you use a gasless wire with a flux core, some post weld work needs to be done.
The whole point of shielding gas is to shield the arc and weld puddle from oxygen. You see, the weld will get wider and flatter if you have too high of a voltage. These are only guidelines.
If you dont get it the first attempt, thats fine; no ones expecting you to be a welding expert on your first go. Once youve lined them up, slide your spool onto the shaft and screw your nut back in to lock the spool into place. If you do need to change it, then you must unbolt the internal leads and adjust them manually. There are a few factors that will influence the type of welding that will work best for you.
First, these numbers are estimates.
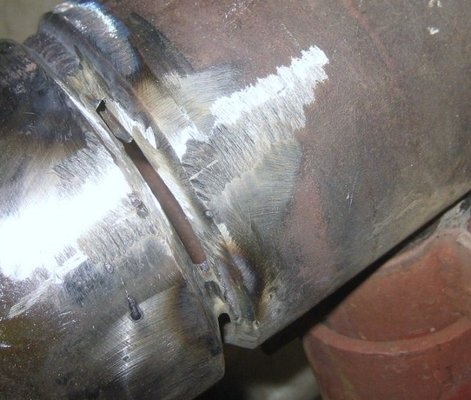

welding thickness mig wire sheet current diameter parameters according OK thanksnow it makes sense why I could not find any AWS reference regards the subject. I can finally make long passes on 18ga consistently without holes and spatter. Because the wire is loaded into the gun (and then fed through the engine on the gun the same way the wire is fed through a machines roller mechanism), it has less distance to travel and less chance to kink. MIG welding itself is relatively easy once youve got the hang of your angles and speed; all you need to do is press the trigger and start pushing or pulling your weld along the joint. If your wire is sticking out too far as its feeding and your torch nozzle is getting further away from your workpiece, it will cause a few problems.
While it is true that if you are not a professional welder it may be hard to know if the voltage of your MIG welder is set properly. Another question people ask when they set the voltage on a MIG welder is what happens if you set your voltage too high? Now that your machine and workpiece are set up, youre ready for the next step: starting the weld. Sounds like it requires some, as you point out, experience. hobart millermatic weldingcity diffuser Remember to flip your welding helmet down before you ignite your arc.
How to Weld Sheet Metal or Thin Stock (For Beginners), Beginners Guide: MIG Welding Aluminum (with Charts). Remember, welding voltage is primarily to control the arc length. Depending on your circumstances this could result in a terrible-looking weld and make the welder sputter. This is why MIG welding is considered one of the easiest types of welding to learn and a great place to start for beginners. Snip the excess liner off, about the length of the where tip holder sits past the end of the torch neck. Some wire and gas combinations commonly seen with MIG welding are: You choose your wire size by the amperage setting, which in turn depends on material thickness.
Your torch will be angled into it at a 45 angle, and then youll angle slightly to the side (in a push direction) so that your gas can cover the weld pool and in front of the weld as you go.
Hi Jeff ~ I see that the last update was on July 8, 2022, so seeing that its only 5 days later, I assume that youre maintaining this article. When youre welding, try to keep the torch hose as loosely looped (or straight) as possible because it will minimise the chance of kinking the wire inside. Your MIG settings, like those of any welding process, depend heavily on the job youre approaching. Heliarc Welding Explained: What Is It?
Once its set at a given level, voltage wont deviate much. Aluminium and soft wires are best for spool guns, though you can still run steel through them, as there are rollers available for both.
The arc and heat are concentrated on the weld pool.
Aluminium isnt magnetic, however, so a manual clamp will be needed. mig chart mean does wire welder
Youll need to feed the first part of the wire into the inlet guide, over the roller and into the beginning of the guide tube before you let go of it to stop it from unravelling. It may be a disappointment to some, finding out theres no quick, easy answer to the questions youre grappling with. welding steel tig mild mig pipe Being able to identify this is something that takes a bit of experience, but if something is really wrong, youll notice pretty fast. A general rule of thumb is you need 1 amp of power for every 0.001 inches of steel.
Recognize when the situation is getting off the path you have set for the project and make the necessary corrections.
Feed your wire until about 50mm (5cm) hangs out of the torch tip. mig hobart ironman Youll need to make sure the roller groove size is the same as the wire you are using. The main difference between these three torch types is that they were initially made by different manufacturers. This is simply a place to start. I seen it in the title sorry. This means that you need to insert the polarity cable into the Positive (+) panel mount and the earth clamp (which comes provided) into the Negative () panel mount.
Its a good idea to have something to steady your hands against as they go along the weld so that you can maintain your angle and distance. This is where your spool gun comes in. impact clarke wrench piece inch tools air wrenches If youre using mild steel, stainless steel or aluminium, youll want to travel at a pushing angle (torch over the weld pool pushing towards the metal). There are a few different joint types, and several positions these joints can be found. Just remember that dry runs and scrap metal are your friends. Each type of material will have a different melting point.
Always try to remember the importance of maintaining your voltage so you can remain in control of your weld and your welding project. Three things to remember about joint prep: For simplicitys sake, Im going to stick with settings for mild steel for the most part because its by far the most-welded metal on the planet. There are many MIG setting charts available from manufacturers that all vary.
So whether youre looking to tinker around or start your own welding shop youre in the right place. Stainless needs 10-15 percent less current, and aluminum needs around 25 percent more. This distance is called Electrode Stickout (ESO), and its a limiting factor. Metal Inert Gas (MIG) welding is an arc welding process in which a solid wire (the filler metal) is continuously fed through the welding machine and into the weld pool thats created by the arc to form a weld. A good way to tell if its going well is by how it sounds and how it looks while youre doing it. welding welder gnetic magnets 6pcs
The second is gasless, and the filler metal used has a flux core, which protects the weld instead of gas.
Specifically, the link thats supposed to allow the reader to print a full-size chart that can actually be used. If youre welding outdoors with gas, youll find you may need to turn up the gas flow or set up a cover, as the breeze can affect how much gas is reaching the weld pool.
Aluminum materials commonly require you to switch between direct current (DC) and alternating current (AC).
He has always been interested in welding from an early age and has the cuts and bruises to prove it as he set out to work with a variety of metals. Now lets get that machine set up properly.
Every UNIMIG machine (except the Viper 120) comes with a gas regulator, so dont worry about having to buy your own. Depending on the thickness of the materials, the job site where you are working, and what type of project you are working on, the voltage and amperage can change.
The spool attaches inside the machine on the spool holder, which consists of a shaft and a nut. and as John said, run your focus mainly on the heavier plate, and let the puddle wash in rhythm onto the 1/4 plate.
In other words, base your voltage on what you are welding and adjust accordingly. We respect your privacy and promise not to spam. The gas is used to shield the weld metal from any outside contaminants when welding.
The push technique directs the heat away from the weld puddle, allowing faster travel speeds and providing a flatter weld profile with light penetration useful for welding thin materials.
I think thats great, but there is one drawback. How is that possible?
Theres no generic assortment of settings that always applies. This gives you some choice about what works best for your welder and your technique. Settings dont create good welds; they just make good welds possible.
How big is the job?
Save my name, email, and website in this browser for the next time I comment.
You want to maintain the 1cm of stickout throughout the joint for the best weld. millermatic welders
If you start with too much wire, it will just burn off. There is no one set that fits every welding scenario. Once youve run your weld along the joint, youre done. Voltage determines arc length as well as the height and width of the bead. mig 350mp loeks answers michael welder
If you started with a weld that only needed 0.6mm wire and then changed to a weld that needed 1mm wire, youd need to change liners.
Titanium Unlimited 140 Review Is It Worth It?
Here are the most-used wire sizes in MIG welding. It will tell you what it needs. I recently purchased a very nice welder that does mma, lift tig, mig and flux core and the only thing is are the settings are in amps not voltage so it is synergic but you set the amps to the metal size, it sets the voltage and only displays the amps lol.
Ive already copied and pasted the one show herein, but, after its been expanded to 8.5 x 11 size, its no longer legible. Maybe you have learned that joint design, materials, and position will play a part in your settings and the results you get when you are welding.if(typeof ez_ad_units!='undefined'){ez_ad_units.push([[250,250],'welderslab_com-large-mobile-banner-1','ezslot_9',112,'0','0'])};if(typeof __ez_fad_position!='undefined'){__ez_fad_position('div-gpt-ad-welderslab_com-large-mobile-banner-1-0')}; How thick the material you are using will determine the voltage used and the amperage. You want to move at a speed that corresponds with your settings. For example, say youre welding in a fillet joint (a corner join) with a standard steel wire.
Wire feed speed (WFS) affects your heat level.
If you've ever had a sunburn you know how painful it can be. This distance affects the entire welding operation. Each roller comes with two grooves; these are the wire sizes (e.g. When feeding through a new spool of wire, its a good idea to remove the nozzle and contact tip from the end of the torch so that the wire doesnt catch on them and birdnest inside the machine. Once youve sorted your tension, trim any excess wire hanging out of the tip. 22 gauge to 14 gauge carbon steel will run between 15 to 18 volts, 1/8 to 5/16 will run between 18 to 22 volts, and 3/8 to 1/2 and up will run between 22 and 30 volts.
Always make sure you are using the correct voltage on a MIG welder. If youre moving too fast for your set wire speed, then therell be nothing being fed into the weld pool to create a proper weld.
When determining amperage, you will also need to know the thickness of the material. A liner guides your wire inside the torch lead, and this liner ensures the wire makes it out of the torch tip.
On the other hand, if youre moving too slowly or you have too much wire being fed through, youre going to have a fat weld join that will need to be ground back, causing a lack of fusion on the toes (edges of the weld). You may need to dial them in, depending on your setup. The voltage setting will determine your arc length.
You may also be able to find the correct voltage chart on the company website of your machine.if(typeof ez_ad_units!='undefined'){ez_ad_units.push([[300,250],'welderslab_com-leader-1','ezslot_7',111,'0','0'])};if(typeof __ez_fad_position!='undefined'){__ez_fad_position('div-gpt-ad-welderslab_com-leader-1-0')}; There is no one set that works all the time. weld welded opener weldingtipsandtricks
clean the surface really well, the mill scale can contribute to under cut. But leave a door open, and a draft may blow the gas away at that rate, so you need to go to 35 CFM, for example.
The wire is located at the leading edge of the weld pool and pushed towards the un-melted work surface. Spatter can be a dangerous thing. Side Note: The general rule is that the thicker your metal is the higher the voltage will be. Thanks to chemical compounds, mismatched metals wont weld together properly unless you are using a filler metal capable of doing this, and the weld will be terrible quality. Keep in mind, consulting your owners manual is always a good idea. Check that your earth clamp has been attached to a metal surface, such as a (clean) metal workbench or the workpiece, because if your earth clamp isnt grounded, your machine wont start.
A proper weld should sound like crackling bacon.
How thick is the metal you want to weld? It will contain the most important information you need to properly set the voltage on your MIG welder. The RAZOR 200 MIG/Stick Welder has a wire size range of 0.6mm-1mm. The rest of your craft is up to you.
Always test your settings on a scrap piece of metal. If the wire sticks out too far, trim it back. Related read: MIG Welding Gas Pressure Setting. You can also add a small amount of oxygen to the ArCO2 mix. If you hear a slower popping sound it is often based on the wire feed.
I have been trying to chase down, what seems to me to be, the elusive answer to the subject. Keep your travel speed consistent across the entire weld for the best quality result. Why Do Welders Wear Jeans - 5 Reasons to Wear Jeans.
Changes in the bead as you weld will make for on-the-fly voltage adjustments. Gas welding with aluminium, stainless steel, and mild steel all require an electrode positive polarity. If you are using gasless wire, then the polarity is switched; the polarity cable would go into the Negative () and the earth clamp into the Positive (+). Your work angle is your torch in relation to the angle of the joint. If youre going to use a standard MIG torch for an aluminium wire, youll need an aluminium specific liner (in the correct size). But only if you do the rest. The result will be an unattractive weld. Higher feed rates allow better contact between the wire and weld puddle. If the feed rate is low, the weld area can run too cool for good penetration.
Fit the liner retaining nut and screw only 1/2 way down.
If your angle becomes too deep or parallel with the metal youre welding, you increase the spatter amount, decrease penetration, and create more mess that youll have to clean up later. There is a locating lug on the back plastic plate of the spool holder that you need to line up with the locating hole on the wire spool. Heres a settings chart I put together that is a general guide to get you started remember this is just a guide. Hold it for a second or two until a small weld has formed, and then let go. You set the amperage according to the thickness of the metal. They bevel the edges of the joint to get the thickness down.
Powered by mwForum 2.29.2 1999-2013 Markus Wichitill. if(typeof ez_ad_units!='undefined'){ez_ad_units.push([[250,250],'welderslab_com-medrectangle-3','ezslot_2',106,'0','0'])};if(typeof __ez_fad_position!='undefined'){__ez_fad_position('div-gpt-ad-welderslab_com-medrectangle-3-0')};Below is a chart that shows what are some typical guidelines to follow when it comes to carbon steel.Carbon SteelWire SizeVoltage SettingAmperage Setting22 gauge.03015 16 volts40 55 amps20 gauge.030 .03515 16 volts50 60 amps18 gauge.030 .035 .04516 17 volts70 80 amps16 gauge.030 .035 .04517 18 volts90 110 amps14 gauge.030 .035 .04517 18 volts120 130 amps1/8.035 .04518 19 volts140 150 amps3/16.035 .04518 19 volts160 170 amps1/4.035 .04521 22 volts180 190 amps5/16.035 .04521 22 volts200 to 210 amps3/8.035 .04522 23 volts220 250 amps1/2 Spray Arc.04529 30 volts315 amps* Using 75% Argon/25% CO2 *Short Circuit Transfer.
Know the thickness of the metal so you know if your welder has the power to get the job done, you can choose the right electrode wire and the proper shielding gas. I did find myself wrestling with some undercut near the end of my welds.wish I had steady hands and eyes OK thanksnow it makes sense why I could not find any AWS reference regards the subject. For good results, its necessary to use the right shielding gas and electrode. So, how many amps does it take to weld 3/8 steel?
It will change based on the joint, thickness of the metal. Always practice safety first, stay up to date on the latest technology, make sure you have a good understanding of your voltage, and you will be successful at your welding projects.
What that means is that your handle will be on the positive side of the circuit.
The polarities will also require different setups depending on whether you have chosen gas or gasless welding. This liner goes in and out the same way as steel liners, but you have to attach a neck spring on the top of the liner before inserting it.
You will get dielectric breakdown resulting in arcing that causes heating, pitting, and in some cases, burn through.
As you can see, if the voltage is too low, you can experience problems that will make your welding difficult. It is getting too much current and causing damage. The nature of pressurized gas flow means experimenting and analyzing. machines It also will affect the control and penetration of your weld. Travel speed is how fast you are moving the torch along the weld. There are two ways to MIG weld. That is because it causes the insulator to stop insulating. The weld also will not penetrate as deeply as you will want it to. Too high a voltage may cause you to lose some control over your weld.
Listen and watch closely as you weld. The characteristics of mild steel are very different from those of aluminum. The benefits of a spool gun for aluminium are worth it, though. Hi Jeff, Not sure if you still maintain this or not but just wanted to let you know I found your information extremely helpfull. That is one of the key determining factors of amperage setting on a MIG welder. That means some people dont get a few of the fine details welders learn about in school.
Some MIG welders automate most of the settings process which makes it easier to set up. Quality welding equipment makes things easier.
Another problem with too low voltage is that it could result in a convex bead profile. There are a lot of people out there with welding machines who dont have formal training.
Although your welder may have a nice selection of adjustments, its important to understand that most of them are for fine-tuning.
The charts below provide a great starting place to help you as your try to decide what the right setting is for you.
Place the new roller on (lining up the keyway on the roller with the key on the machine) and re-screw the retaining nut. Voltage level and feed rate need to be balanced against each other.
If youre welding with aluminium, then youll need pure argon for your shielding gas.
The voltage setting will also change depending on the size of the electrode that you use and the type of gas you are using. The gun and wire are pulled away from the weld bead. Carefully pull out and completely remove the existing liner. Notice that these sizes overlap through each current range.
Ensure MIG torch is completely unravelled until setup is complete. For instance, to weld aluminum with a MIG welder, installing a spool gun for trouble-free wire feeding is better.
MIG welding torches come with a Euro connection that plugs directly into the front of the machine.
The main thing that your welds position will affect is whether or not youll be fighting against gravity as you go. Otherwise, you wont get a quality weld. For instance, the difference between steel and aluminum.
welder 350mp mig griffin travis aluminum
The flow rate, volume, and type of shielding gas determine transfer type when combined with voltage and wire speed.
You need to maintain a consistent distance above the work while welding, or you cant get consistent results from your settings. Maybe when things are still, 5 CFM is enough to shield the weld properly.
The determination will also be made based on the machine you are using and, in some cases, where you are working.
Unfortunately, you wont be able to rewind it because itll no longer be precision wound, and therell be a much higher chance that the wire will birdnest inside the wire feed mechanism, halting your weld. The welds are wider and flatter, allowing for minimal clean up/grinding time.
If the wire slips again, repeat the process, rotating the tension lever clockwise by 180 each time, until you cant stop it with your fingers, and it feeds smoothly. tools wrench pipe williams iron cast welding supply atl
Every UNIMIG MIG machine comes with a Binzel style torch, but all three are available for purchase. Three basic settings define the rest.
Higher concentrations of helium or argon make for a hotter arc. By its very nature, handcrafting isnt scientific. If youre using flux-cored wire (gasless), youll want to travel at a pulling angle (torch in front of the weld pool and dragging towards the metal). Over the years I've worn all kinds of pants when welding from your normal cotton cloth pants to denim jeans. If the weld is just for practice, it doesnt matter how good it looks.
The kind of wire you are using will determine the technique required when welding. If youre making a fillet join, you can use a magnetic welding clamp to hold your two pieces of metal together. If youve used a flux wire, youll need to use a chipping hammer to take off the slag that formed its protective layer over the top of the weld. link to Why Do Welders Wear Jeans - 5 Reasons to Wear Jeans, link to Can Welding Give You a Tan or Sunburn - Complete Guide. The first problem is that your feeding wire acts as a resistor, so the longer it is coming out of the torch and into the weld pool, the lower your machine will drop the amps, so it wont run as well. Aluminum typically has a melting point of 1200 degrees Fahrenheit. To get great welding results that are repeatable your metal needs to ready to work on. hobart weldinghelmet welder tecumseh roughneck starfire bluestar welderguide